GENERAL BUILDING INFORMATION |
BUILDING NAME |
|
Susquehanna Health Patient Tower Expansion |
LOCATION |
|
724 Campbell Street, Williamsport, PA 17701 |
PRIMARY OCCUPANTS |
|
Susquehanna Health, Healthcare |
GROSS BUILDING AREA |
|
243,000 SQFT |
NUMBER OF STORIES |
|
6 Stories Above Ground |
CONSTRUCTION DATES |
|
10/22/2009 - 9/19/2012 |
CONTRACTED GMP AMOUNT |
|
$82,297,101.00 |
APPROVED CHANGE ORDERS |
|
$6,598,072.00 |
PROJECT DELIVERY METHOD |
|
Single Prime GMP - Design-Bid-Build |
|
|
PROJECT TEAM DIRECTORY |
OWNER |
|
SUSQUEHANNA HEALTH |
|
CONSTRUCTION MANAGER |
|
L.F. DRISCOLL CO. LLC. |
|
ARCHITECT |
|
GRANARY ASSOCIATES |
|
STRUCTURAL ENGINEER |
|
O'DONNEL & NACCARATO |
|
MECHANICAL ENGINEER |
|
PWI INC. |
|
CIVIL ENGINEER |
|
LARSON DESIGN GROUP |
|
|
|
ARCHITECTURE |
Susquehanna heath is a three-hospital system that hasn’t had a major renovation or construction project within the last 20 years. The patient tower expansion project is the fourth phase of Susquehanna Health’s Project 2012 initiative. This $250 million initiative was launched in 2006 with the intent to update and renovate the outdated existing facilities as well as clean up the surrounding community. It is Susquehanna’s vision to be up-to-date medical facility as well as being a beacon of healthcare.
Designed to be the entrance for Williamsport regional medical center, the new patient tower faces and overlooks the city. This design shows how much Susquehanna Health cares about the community because in previous years the building had pointed away from the city almost shunning it. The building was designed to become a visible landmark and to reach out to the community. This six-story 243,000 square foot tower features 84 single-occupancy rooms, increase privacy, and improved patient care. Private rooms provide an environment in which confidential patient history information is easily accessed and enables the isolation of patients to prevent transmission of infection.
The patent tower also features a two-story entrance for expanded emergency and imaging departments the Second floor houses new intensive care and critical care units and a high-tech education and innovation center. The third floor is comprised of surgical areas with new operating rooms. The fourth floor on the other hand houses orthopedics and spine research and surgical areas.

(Pictures Provided by L.F. Driscoll.)
|
ARCHITECTURE - MAJOR CODE AND HISTORICAL REQUIREMENTS |
GUIDELINES FOR DESIGN AND CONSTRUCTION OF HEALTH CARE FACILITIES NFPA 101 LIFE SAFETY CODE
INTERNATIONAL BUILDING CODE (IBC)-NONAPPLICABLE FOR LIFE SAFETY
ICC ELECTRICAL CODE
INTERNATIONAL ENERGY CONSERVATION CODE
INTERNATIONAL EXISTING BUILDING CODE
INTERNATIONAL FUEL GAS CODE
INTERNATIONAL MECHANICAL CODE
INTERNATIONAL PERFORMANCE CODE FOR BUILDINGS AND FACILITIES
INTERNATIONAL FIRE CODE
ICC/ANSI A117.1 ACCESSIBLE AND USABLE BUILDING AND FACILITIES
|
202006
2000
22006
2006
2006
2006
2006
2006
2006
2003
|
*NO HISTORICAL REQUIREMENTS APPLY TO THIS BUILDING*
|
ARCHITECTURE - ZONING REQUIREMENTS |
ZONING DISTRICT
MINIMUM LOT SIZE
MINIMUM LOT WIDTH
MINIMUM LOT DEPTH
FRONT YARD SETBACK
REAR YARD SETBACK
SIDE YARD SETBACK
COMBINED SIDE YARDS
MAXIMUM FLOOR RATIO |
INST-INSTITUTIONAL DISTRICT
10,000 SQFT
80'
100'
25'
25'
20'
40'
1.5
|
BUILDING ENCLOSURE |
The building enclosure consists of many different components that make up the building’s façade and roof. As seen in the figure below, the white towers of the façade are constructed out of architectural precast concrete. The south façade is also constructed out of precast concrete however, this facade consists of a thin brick faced precast as well as 3” foam insulated core metal panels. Another integral part of the building’s enclosure is the curtain wall which can be found on the eastern entrance. The curtain walls in conjunction with the many windows which encompass the entire building, serve the vital function of providing natural light to the patients. All windows and curtain walls for this project are either made of 1” insulated vision glass or 1” insulated spandrel.

(Pictures Provided by L.F. Driscoll.)
Similar to the Façade, the roof is also comprised of many different elements. Although each roof may be different, they all start with a lightweight metal composite deck with a 6 1/4” concrete slab on top. Roofs are also sealed with EPDM roof membrane which is adhered to 2” foam plastic insulation. Four of the five roofs are covered with vegetation thus making them green roofs.
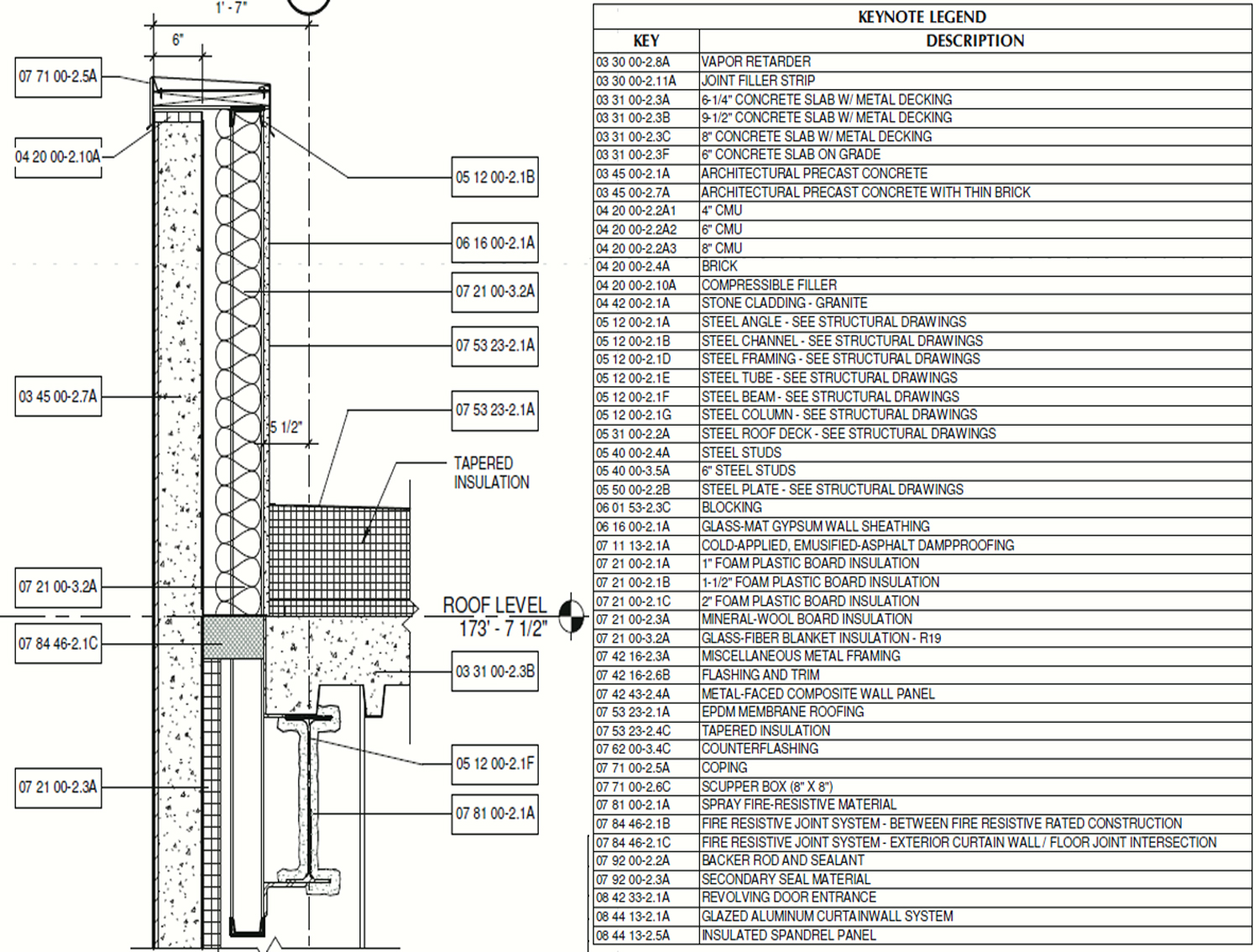
|
SUSTAINABILITY FEATURES |
Susquehanna Health in cooperation with L.F. Driscoll, Granarty Associates, and Stantec Architecture, Inc. are designing this building to comply with certain U.S. Green Building Council (USGBC) LEED prerequisites and credits to obtain a LEED for Health Care (LEED-HC) ranking . This project will be designed to meet LEED-HC however; it will never receive an official LEED seal of certification. After being designed, Susquehanna Health realized that there were huge costs associated with hiring LEED consultants. They opted not to hire the consultants and instead to reinvest that money back into the project.
Sustainable design features that are incorporated the Susquehanna Health Patient Tower Expansion include green roofs, sloped roofing having appropriate Solar Reflectance Index (SRI), specialized cooling towers, and glazing applied to the large curtain walls and windows.

(Pictures Provided by L.F. Driscoll.)
Key sustainable construction practices include proper waste management, heavy recycling, and securing regional materials. In addition to construction practices, many credits are also being earned by using LEED certified materials. Some of these materials include rapidly renewable biobased products, insulated metal panels and low volatile organic compound (VOC) based products. One of the main LEED objectives for this project is achieving an acceptable indoor air quality. This means the elimination of VOC’s, bioaccumulative toxic chemicals, and cement that was fired from kilns with hazardous waste. |